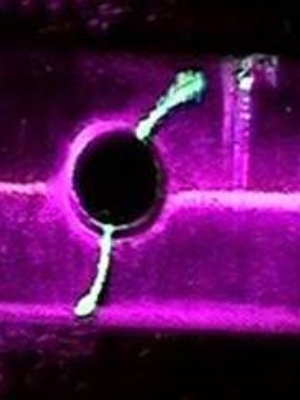
Yazar : Sedat Nevzat Aras NDT lvl:3
TAHRİBATSIZ MUAYENE
(Non Destructive Testing )
Giriş
Tahribatsız Muayene ;
Adından anlaşılacağı üzere ,Ürünün muayenesi sonucu her hangi bir sorunu olmadığına karar verildiğinde servise verilebileceği anlamına gelir . Tahribatlı muayeneyle farklılığı burada başlar.Tahribatlı muayene uygulanan ürün işlevine devam edemez amaç İmalat kalitesi ve ürünün ait olduğu gurupla ilgili değerlendirme yapmaktır.Benzetme yapmak gerekirse Tıp alanında cerrahi müdahale Tahribatlı muayene,Dahiliye Uzmanının Muayenesi Tahribatsız Muayenedir.
1.SÜREKSİZLİK VE HATA
Bir bütünün doğal yapısını kesintiye uğratan her türlü oluşum süreksizliktir. Süreksizliğin hata olup olmadığına ; o konuda kullanılan Şartname , Standart yada müşteriyle yapılan özel sözleşme de yer alan Limitler değerlendirilerek karar verilir.Bu bağlamda Her hata bir Süreksizlik ama Her süreksizlik bir Hata değildir. Diyebiliriz.
Kabul / Ret kriterinde Limitlerin değerlendirilmesi gerekir.
2.TAHRİBATSIZ MUAYENE UYGULAMA GEREKÇELERİ
a.Kalite
Bilindiği üzere her müşteri aldığı ürünün bedeli karşılığında ürün kalitesi ister.Rekabet ortamında aldığı bir ürünün kısa bir süre sonra kırılması yada Kaynağında kopma meydana gelmesi Üretici firma garantisinde olsa dahi müşteri görüşü olumsuz etkilenecektir.
Ürünün pazara sunulmadan önce Tahribatsız muayeneye tabi tutulması sonradan oluşabilecek hataları erken tesbit ederek hatalı. bir anlamda kalitesiz ürünün pazara sunulmasını engelleyecektir.
b.Güvenilirlik
Ürünün kullanılmaya başladıktan sonra güvenilir olması vazgeçilmez kuraldır.Tonlarca yüke maruz kalacak bir vinç kancası ve zincirin,Bir uçağın türbinindeki bir pal’in, Dişli gurubundaki bir tek dişlinin,Nükleer santraldaki soğutma sisteminde yer alan bir borunun yerine getirdiği görevi düşünürsek ; Güvenilirliğin önemini daha iyi kavramış oluruz.
Malzemede oluşacak bir hata sadece kendisini değil tüm sistem yada aracı olumsuz etkileyecek ,Buna bağlı olarak ekonomik zarara ,insanla direk ilişkili bir kullanımdaysa can kaybına neden olacaktır.Bu nedenler göz önüne alındığında gerek üretimde gerek servis sürecinde tahribatsız muayene kullanımı riskleri azaltıcı bir faktör olacaktır.
c.Üretim maliyeti
Serbest Pazar ekonomilerinde ve rekabetin olduğu her alanda Üretici, üretim maliyetini göz önünde bulundurmak zorundadır.
İlk bakışta üretim hattının sonuna yada Üretimin değişik adımlarında Tahribatsız Muayene istasyonu kurulması yatırım maliyetini yükseltmiş olsada bir süre sonra kendisini amorti edecek yada düşük maliyetli bir işlem haline dönüşecektir.Ancak bu düşüncenin geçerli olabilmesi için ;Tahribatsız muayene ile ilgili teçhizatın kapasite kullanımının yüksek olması gerekmektedir.Az sayıda üretim yapan işletmenin Tahribatsız muayene hizmetini dışardan satın alması daha ekonomik bir uygulama olacaktır.
Kütük malzemeyi dış alımla temin eden bir fabrikanın ,üretim araçlarını kullanarak dişliler ürettiğini varsayalım. Üretim ön işlem aşamasında
( Kesme,Tornalama,Freze işlemi,delik ve kama kanalı açma,ısıl işlem,yüzey temizleme,Markalama, Koruyucu kaplama ,paketleme,stoklama vs.)gerçekleşiyorsa bir tek ürün; Maliyet yönüyle hammadde.işçilik dışında amortisman, Aydınlatma ,ısıtma ,soğutma ,stoklama,güvenlik,kira gibi onlarca gider kaleminden pay alır.Bu ürün hatalı (Çatlak) olarak pazara ulaşırsa tüm maliyetler zarar hanesine yazılır. Oysa her işlem aşaması arasında Tahribatsız muayeneye tabi tutulsa hata tespit edildiği andan sonraki maliyetler ortadan kaldırılmış olacaktır.
d.Çabuk ve Kolay Uygulama :
Tahribatsız muayene ;diğer üretim işlemlerini kesintiye uğratmadan ve seri üretimde uygulanabilir .Muayene sonucu çabuk alınır ve kesindir.Otomasyona uyarlanabilir.Özellikle son dönemde üretilen cihazlar seri üretimde kullanılacak şekilde dizayn edilmiştir. Ürünle ilgili muayene işleminin sonucu kayıt altına alınıp saklanılabilir. Tahribatsız muayene yöntemleri yukarda bahsedilen gerekçelerden başka amaçlar içinde kullanılabilir. Güvenlik ,İnşaat ve Tıp bu konuda örnek olarak gösterilebilir.
3.MUAYENE YÖNTEMLERİ
Her hangi bir malzemeye işlevini yerine getirmesine engel olacak bir zarar vermeden yaptığınız her türlü muayene işlemi genel anlamda Tahribatsız Muayene olarak adlandırılır.Bu nedenle rakam vererek şu kadar sayıda tahribatsız muayene yöntemi vardır demek doğru bir bilgilendirme olmayacaktır.
Karşılaşabileceğimiz temel yöntemleri Hacim yöntemleri ve Yüzey yöntemleri olarak sınıflandırabiliriz.
Yüzey yöntemleri : Adındanda anlaşılacağı üzere Yüzeyde yada yüzeye yakın süreksizlikleri tesbit etmekte kullanılabilir.Bunlar;
Gözle Muayene ,(VT)
Penetrant,(PT)
Manyetik Parçacık,(MT)
Eddy – Current,(ET)
Hacimsel yöntemler : Yüzeyde ve yüzeyin altında bulunan süreksizlikleri tesbit etmekde kullanılır.Bunlar;
Ultrasonik Test,(UT)
Radyografik Test (RT)
Aküstik emisyon Testi (AT)
Kaçak testi
Termografik Test
Tüm uygulanan testlerde beklentiler;
Süreksizliği bulmak,Yerini ve Boyutunu belirlemektir.
Bunlarla beraber bazı teknikler metalurjik yapıyla ilgili bilgiler verebilir.
Sertlik ölçümü Yarı tahribatlı olarak adlandırılabilir.Malzemenin direnci ve gerilimiyle ilgili bilgi verir.
Farklı dokümanlarda ; tercüme ve adapte yapan kişiler farklı adlandırmalarda bulunmuşlardır.Bu nedenle türkçeleştirilmiş kaynaklarda ;Sıvı girinim,Girdap akımları , Ultrases gibi kavramlarla karşılaştığımızda bunların yukarı adı geçenlerle aynı olduğunu bilmeliyiz.Ancak bazı terimleri Türkçeye çeviri yapmak yerine olduğu gibi öğrenmekde yarar vardır.
4.YÖNTEM SEÇİMİ
Unutulmaması gereken en önemli konu her zaman geçerli olan adı geçen ürünle ilgili olan Şartname ve teknik dokümanlardır.Biz burada yöntemin seçilmesi sırasında dikkat edilen konulardan bahsedeceğiz.
4.1.Ekonomik olmak (maliyet)
Ürün kontrolunda tüm yöntemler uygulanabiliyorsa üretim maliyeti en düşük olan seçilmelidir.Piyasa şartlarında maliyet düşürülemediğinde rekabet şartları işletme açısından güçleşmektedir.
4.2.Güvenilir olmak
Uygulanan Tahribatsız muayene test’ i sonucunda uygulayıcıda
- Acaba ? sorusu oluşmamalı, Verilen karar net olmalıdır. Eğer yöntem güvenilir değil ise Hatalı bir ürüne sağlam,Hatasız bir ürüne hatalı raporu vermek gibi olasılık her zaman vardır.yapılan bu hataların sonucu bazen parasal zarara bazen can kaybına neden olabilir .
4.3.Uygulanabilir olmak
Operatörün kontrol edemediği değişkenlerden; Test malzemesinin geometrik ve fiziki yapısı, Malzeme cinsi,Çalışılan yerin özellikleri gibi gerekçeler Muayene yönteminin seçiminde sınırlayıcı olmaktadır .Bu konuyla ilgili olarak Yöntemlerin anlatılması sırasında Avantajlar-Dezavantajlar olarak detaylı açıklamalar yapılacaktır.
4.4.Tekrarlanabilir olmak
Uygulanan test işleminin sonucu Farklı mekan ve farklı zamanda aynı parametreler kullanılarak tekrarlandığında aynı olmalıdır.Örneğin Tedarikçi bir firmadan ki bu yurtdışı firmada olabilir,getirilen kütük seklindeki bir ürünün kabulü sırasında Tahribatsız muayene yöntemi kullanarak hata tespit ettiniz.Ürünü iade ettiğiniz işletmede aynı yöntem uygulandığında farklı mekanda farklı operatör ve farklı techizatla aynı sonuç alınabilmelidir.
4.5. İnsan ve Çevre sağlığına uygun olmalı
Gerekli tedbirler alınması halinde kullanılan teçhizatın ve sarf edilen malzemelerin uygulayıcıya ve çevreye zarar vermemesi gerekir.
5.YÖNTEMİN UYGULANMASI İÇİN GEREKLİ ŞARTLAR
Herhangi bir tahribatsız muayene yönteminin uygulanabilmesi için olması gerek üç temel şart vardır.Bunlardan birinin olmaması veya yeterli olmaması uygulama işleminin geçerliliğini ortadan kaldıracaktır.Bunlar;
1.Personel
2.Teknik donanım(Techizat)
3.Teknik doküman. dır.
5.1.Personel
Uygulayıcı personelin hangi yöntemi hangi seviyede uygulayacağı belirlenmeli ve o seviyeye uygun eğitim verilerek Vasıflandırılmalı ,ölçme değerlendirmeye tabi tutularak başarılı olduğu takdirde Sertifikalandırılmalıdır .Bu şartları yerine getirmeyen uygulayıcının yaptığı kontrol geçerli değildir. Tahribatsız Muayene Personelinin Vasıflandırılması ve Sertifikalandırılması şartları hem ulusal hem uluslar arası kuruluşlar tarafından belirlenmiştir.(Nas 410,En 4179.ISO 9712.)
(Göz raporu olmalı,Renk körü olmamalıdır.)
5.2.Teknik donanım(Teçhizat)
Toplumumuzda kullandığımız bir atasözü bu konuyu çok iyi açıklamaktadır “ Alet işler,El öğünür “Personel ne kadar eğitimli ve tecrübeli olursa olsun o yöntemi uygulamak için gerekli cihaz ve teçhizat(Bunlarında Kalibreli , Proses kontrolları yapılmış ve ilgili şartnameye uygun olması gereklidir)yoksa veya yeterli değilse yine uygulama olanaksız yada geçersizdir.
3.Teknik doküman.
“ Ne aradığını bilmeyen aradığını asla bulamaz” deyiminde olduğu gibi uygulamaya başlamadan önce Hangi özellikteki malzemede ,Hangi yöntemle ,Hangi bölgede ,Ne tür ve hangi büyüklükte süreksizlikler aramamız gerektiğini, eğer limit verilmişse hangi ürünün Ret veya Tamir edileceğini,hangi Ürünün Kabul edileceğini şüpheye yer bırakmayacak şekilde açıklayan Teknik doküman,Şartname veya Özel teknik sözleşme gerekli şartlardan birisidir.
Bazı test işleminde ana yöntem ve ardından doğrulama yöntemi istenir.Doğrulama yöntemi genelde farklı bir yöntem olur.Örneğin Penetrant Test işlemi sonucu bulduğunuz bir süreksizliğin Eddy-Current Testiyle teyit etmeniz gerekebilir.
Tahribatsız Muayene konusuna genel anlamda göz gezdirmiş olduk.
Bundan sonraki aşama Her bir yöntemle ilgili Teorik ve Uygulamalı Eğitime
Yönelik çalışmalar olacaktır.
SIVI PENETRANT KONTROL METODU
Sıvı penetrant metodu Tahribatsız muayene metot guruplamasında yüzey metotlarından biridir.Adından da anlaşılacağı üzere sadece yüzeye açılan süreksizlikleri tesbit edebileceğimiz metotdur.
Bu süreksizlikler; Çatlaklar,Dikişler,Haddede veya Dövmede meydana gelen katlanmalar,Gözenekler ve malzeme içerisine saplanmış farklı madde yapıları olabilir.
Çok büyük gözenekli yapıya sahip olmamaları şartıyla Metallere,Seramiklere,Plastiklere kısaca kimyasal olarak zarar görmeyecek her türlü materyale uygulanabilir.
Tahribatsız muayene metotlarının ilk uygulananıdır.1800 lü yıllarda ilk uygulaması Demiryolları bakım atölyelerinde yapılmıştır.Test edilecek malzeme kullanılmış yani siyah yağ kazanına daldırılıyor,yağın malzemeye işlemesi süresince bekleniyor daha sonra malzeme gaz yağıyla temizlendikten sonra üzerine tebeşir tozu tatbik ediliyor.Tebeşir tozunun üzerine yağ çıkarsa çatlak olduğuna karar veriliyordu o zaman verilen ad yağ ve beyazlatma metoduydu
Zamanla kullanılmış yağ yerine içine boya katılmış yağ,1941 yılındada Floresan madde ilave edilerek kullanılmaya başlandı.
SIVI PENETRANT KONTROL METODU TEMEL PRENSİBİ
Yer çekimi kanunu düşündüğümüzde kütlesi olan tüm varlıklar dünyanın merkezine doğru hareket ederler.Ancak;Gaz lambasında ki gaz fitilden yukarı doğru gider,Evlerin zemin katlarında temelden yukarı doğru giden su yada yağmurlu havada yerde az bir su olmasına rağmen su pantolon paçasından çok yukarı doğru hareket eder.
Tüm bu ilk anda ters gelen bu olayların nedeni Kapiler harekettir . (capilarity).Kapiler hareketi tanımlamanın en basit yolu;Katılarla karşılaşan sıvılar tırmanma eğilimindedir.Kapiler hareketi etkileyen parametreler ise;
Birleşme(Cohezyon),
Yapışma (Adhezyon),
Yüzey gerilimi(Surface tension)
Akışkanlığa(Vıscosıty) bağlıdır.
İlk olarak sıvının ıslatma kabiliyetinden söz etmemiz gerekiyor.
Sıvı katı bir yüzeye temas ettiğinde ,sıvı molekülleri ile yüzey arasında bir yapışma kuvveti söz konusu olur.sıvının yüzey gerilimi bu yapışmanın, buna ıslatmada diyebiliriz gücüne karar verir.bunu daha iyi açıklayabilmek için sıvı ile katı arasında oluşan kontak açısını inceleyelim
Kontak açısı küçüldükce ıslatma kabiliyeti artmaktadır.
Birinci şekilde gösterilen sıvı damlası hiç bir yapışma özelliği göstermez.Cıva gibi düşünebiliriz.,ikinci şekilde sadece duracak kadar yapışma kuvveti var koyu bir Bal damlası gibi düşünebiliriz,Üçüncü şekil ise bulunduğu yüzeye yayılan bir sıvı su olabilir.....Bunlardan hangisi bizim kontrol metodunda kullanacağımız sıvı olan Penetrantın özelliğine uygundur?
(Penetrant ingilizceden alıntı olup Penetration yani nufuz etme anlamından gelmiştir)
Yukarıda damla olarak gördüğümüz sıvı dolu kap içerisine ince bir cam boru soktuğumuzda;
Penetrantın taşıması gereken özellik ;Düşük yüzey gerilimine ve yüksek ıslatma kabiliyetine sahip olmasıdır.
Penetrant uygulamasının tercih edilmesinin gerekcesi;Maliyeti düşüktür,Portatif techizatla atölye dışında uygulama yapılabilir ayrıca Yüzeye açılan süreksizlik tesbiti dışında Tanklarda,depolarda bir yüzeyden uygulayarak diğer yüzeyden kontrol ederek sızıntı testi yapabilme olanağı sunar.
Penetrantın diğer fiziksel özellikleri ise;
Viskozite: Viskozite damıtılmış suyun akışkanlığına oran dersek.Viskozitesi düşük olursa girinimi hızlı olur.ancak yeterli girinim olmadan yüzeyden akabilir.
Özgül Ağırlık(Spesific gravity):Damıtılmış suya göre oran.Sudan düşük olduğu için su tankın içinde dibe çöker.
Parlama noktası(Flash point): Parlama noktası SAE AMS 2644 e göre minimum 93 0 C olmalıdır.
Kaynama ,Buharlaşma noktası(Volatılıty) yüksek olması istenir nedeni ise buharlaşma nedeniyle ekonomik kayıp,Kimyasal buharın sağlık açısından zararı(Toksin)ve alev alması buharlaşma olursa daha kolay olur.
Ayrıca bilinmesi gereken ;Depolama şartlarında direk güneş ışığına maruz kalmamalı ve 0 0 c ile 55 0 c arasında depolanmalıdır.
PENETRANT UYGULANMASI İÇİN YÜZEY HAZIRLAMA İŞLEMİ:
Tanımımızda “Yüzeye açılan süreksizlik” sınırlamasını belirtmiştik.Bu nedenle Penetrantın süreksizlik içerisine nufuz etmesine engel olacak Boya,Pas,Yağ,Su ve Yabancı madde yüzeyde bulunmamalı,var olanlarda temizlenmelidir.Penetrantın nüfuz etmesine engel kaplamalarda temizlenmelidir.
Temizleme işlemini başka bir birim dahi yapsa sorumluluk NDT teknisyenine aitdir.Çünki sonuç rapor sorumluluğu ona aidtir.
Yapılacak işlemleri aşağıdaki şekilde sıralayabiliriz.
1.Boyanmış malzemede boya sökme işlemi:
Amaç sadece boyayı sökmek değil,aynı zamanda bu işlemi Test malzemesine zarar vermeden gerçekleştirmektir.
a) Plastik medya kullanarak mekanik boya sökme işlemi:
Özel olarak imal edilmiş Kumlama makinalarında,Boyadan daha sert,Test malzemesinden daha yumuşak granül halde bulunan plastik partiküller basınçlı hava kullanılarak boya üzerine çarptırılırlar,boya katmanı parçalanır.Yüzeyden boya söküldükten sonra parça yıkanır ve kurutulur.
b) Kimyasal boya sökücü kullanarak boya sökme işlemi:
Piyasa alımıyla bulunabilen boya sökücüler kullanılabilir.Bölgesel olarak Fırça ile tatbik edilebilirler veya kazanlarda bulunan boya sökücü içerisine test parçası daldırılabilir.Dikkat edilmesi gereken konu;Boya sökücüler genellikle asit ihtiva ederler.Bu nedenle boya sökülebilir hale geldiğinde fazla bekletilmeden temizlenmelidir aksi halde Test malzemesine zarar verebilir.
2)Dağlama işlemi:
Mağnezyum,Aluminyum benzeri metallerde makina işlemi uygulandığında kesici takım sıvama işlemiyle süreksizliğin üzerini kapatabilir.Bu nedenle bu tür malzemeler kontrol öncesi seyreltik asitle dağlanır.Asit yüzeye tatbik edilir,Belirli süre beklenir( 10 dakika) ve suyla yıkanır,kurutulur.
3)Deterjanla temizleme işlemi:
Tüm test malzemelerine uygulanabilir.Önemli olan temizleme işlemi;Daldırma,silme veya basınçlı makinayla yıkama olsada işlem bittikten sonra deterjandan arındırılıp kurutulmalıdır.Nedeni ise Korozyon oluşmasına engel olmaktır.
4) Buharla temizleme ve yağ giderme işlemi:
Buhar en etkin temizleme yöntemlerinden biridir.Isı nedeniyle yağları çözer ve temizler,Test parçasını ısıtması nedeniyle süreksizlik içerindeki suyuda buharlaşma sırasında dışarı atar,uygun test yüzeyi hazırlar.
5) Ultrasonik temizleme işlemi:
Kazan içerisinde bulunan üreticinin tavsiya ettiği deterjan ilave edildiğinde yağları çözer.Buna ilave olarak kazan dışından Proplar vasıtasıyla deterjan-su karışımına gönderilen ultrasonik titreşimlerle karbon birikintilerini temizler.Özellikle cıvataların diş diplerini temizlemekde oldukca etkindir.
-Ultrasonik temizleme cihazları
6) Test malzemesi üzerindeki Pas ve Pullanmaların temizlenmesi:
Bu işlem için “Pas sökücü” örneğin WD 40 tatbik edilir ve test malzemesinden daha yumuşak bir malzemeyle ovalama işlemi yapılır.Örneğin Çelik malzeme üzerinde Aluminyum bulaşık teli,Aluminyum malzeme üzerinde skoçbrayt kullanılabilir.Yukarıda bahsedilen yöntemlerden birini veya birkaçını kullanarak;Test malzemesine zarar vermeden yüzeyinde Boya,Yağ,Pas,artık madde v.s. bulunmayan kuru yüzeye sahip bir Test malzemesi hazırlandı....
PENETRANTIN UYGULANMASI :
Penetrantı uygulayacağız ama nasıl bir Penetrant?
-Test malzemesinin boyutu ne?
-Küçük bir alan mı kontrol edilecek?
-Hava sıcaklığı nedir?
-Karanlık odamı kullanılacak yoksa açık alandamı çalışacağız ?
-Hangi Tip penetrant kullanacağız?
-Kullandığımız penetrantın temizleme yöntemi ne olacak?
-Kullandığımız penetrantın hassasiyet seviyesinin ne olmasını istiyoruz?
Bu soruların yanıtlarını vermeden işe başlayamayız.En kolay işlem Standardın istediğini uygulamaktır.
PENETRANT ÇEŞİTLERİ
Penetrantla ilgili ilk sınıflandırma ne şekilde görülebileceğiyle ilgilidir.
Bu sınıflandırmada “Tip” olarak adlandırılmıştır.
Tip 1 Floresan penetrant (Ultraviole lambayla görülebilir)
Tip 2 Görülür penetrant (Gözle görülebilir)
Tip 3 Çift hassasiyetli penetrant (Hem gözle hem UV ile görülebilir)
Tip 1 Floresan penetrant Uygulamasında dikkat edilmesi gereken;
-Kullanılan Penetrantın son kullanım tarihinin geçmemiş olması gerekir. Genellikle karartılmış veya yarı karartılmış ortamlarda 320 - 400 nanometreler arasında dalga boyuna sahip siyah ışık altında görülür. Süreksizlikler büyük olmaları dışında, beyaz ışık altında görülmezler.
-Kullanacağımız UV lamba ışık şiddeti zamana bağlı olarak azaldığından,Test öncesi 38 Cm mesafeden 1000 güce sahip olmalıdır.
Test işlemi karanlık odada olmadığı durumlarda ışık şiddeti değişir.Ortamın karanlık veya loş olması durumunda 20-50 mikron genişliğinde süreksizliktesbit edilebilir fakat aydınlık ortamda 5000 ışık şıddetine gereksinim vardır.
Uygulayacağımız Floresan penetrant basınçlı kutu içerisinde(Sprey) veya kazan içerisinde olabilir.
Amaç Test edilecek malzeme üzerine penetrantı uygulamaktır.Büyük bir parçada belirli bir kritik alanı kontrol edeceksek sadece anılan bölgeye fırçayla tatbik etmek ekonomik olacaktır.
Test parçasına uygun bulduğumuz yöntemle (Daldırma,Fırça,Sprey vs.)..........
Tip 2 : Görülebilir penetrant :
Adındanda anlaşılacağı üzere test işlemini UV lamba kullanmadan yani yalın gözle göreceğimiz kontrola olanak sağlayan penetrant türüdür.(Sertifikasyon için neden göz raporu istendiğinin gerekçelerinden birisi ortaya çıkıyor)
Renk olarak kırmızı renklidir.Havacılık sektöründe kullanımı yasaklanmıştır.Spot-Chek kontrolunda kalem şeklinde olan türleride vardır.
Aynı şekilde temizlenmiş yüzeye tatbik ediyoruz.......
Tip 2 :Çift hassasiyetli penetrant :
Aynı anda Gözle ve Ultraviole lambayla görülebilen penetrant türü.
NOT: Bunların dışında oksijen sistemlerinde kullanılabilcek özel penetrantlar üretilmiştir.
PENETRANT HASSASİYET SEVİYELERİ:
Uygulama öncesi standardın bizden istediği hassasiyet seviyesine uygun penetrantı seçerek kullanmamız gerekir.
Hassasiyet seviyeleri;
Hassasiyet seviyesi ½ Çok düşük hassasiyet
Hassasiyet seviyesi 1 Düşük hassasiyet
Hassasiyet seviyesi 2 Orta hassasiyet
Hassasiyet seviyesi 3 Yüksek hassasiyet
Hassasiyet seviyesi 4 Çok yüksek hassasiyet
PENETRANT BEKLEME ZAMANI
Penetrantın bekleme zamanı Penetrantın parçanın yüzeyinde kaldığı toplam süredir.Kontrol işleminde önemlidir.Penetrantın süreksizliğin içerisine nufuz edebilmesi için zamana gereksinimi vardır.Ancak zaman çok fazla olursa penetrant kuruyabileceğinden uygun süre beklemesi gerekir.Bekleme zamanı genellikle kullanılan standartda belirtilmiştir.Nufuziyet zamanını etkileyen bazı değişkenler vardır.Bunlar;
*Penetrantın yüzey gerilimi,
*Penetrantın temas açısı.
*Viskozite
*Atmosferik basınç,
*Süreksizlik -Penetrant arasında sıkışan basınç,
*Süreksizlik duvar yapısının radyüsü ve derinliği
*Penetrantın spesifik gravitesi veya yoğunluğu,
*Penetrantın mikro yapısal özellikleri gibi.
İdeal bekleme zamanı denemeler sonucu belirlenmiştir ve Uygulama türüne göre değişiklik gösterir.Penetrant kurumadığı sürece bekleme zamanının uzun olmasında hiç bir sakınca yoktur
Ancak bilmemiz gereken ;
Gerçek bekleme süresi için teknik şartnameye bakmamız gerektiğidir..
Aşağıdaki tabloda beklenen süreksizlik türüne göre örnek bekleme süreleri verilmiştir.
Pürkürtme,Dökme,Fırçayla veya Kazan içerisine test parçasını daldırarak yüzyin penetrantla kaplanmasını sağlamış ve Standardın ön gördüğü şekilde Penetrant süreksizliğin içerisine tamamen girinceye kadar bekleme süresini doldurduk. Bu arada başka işlerde yapmamız gerekebilir.Süreyi geçirebilirdik geçtiğimizi varsayarsak; Yüzeye yeniden Penetrant tatbik ederek işlemi yeniden başlatmamız gerekir.Buna ilave olarak bilmemiz gereken Test parçasının ve Penetrantın ısısının 12 0 C ile 52 0 C arasında olması gerekir .
Sistemimizde olması gereken techizatlardan biriside Alarm özelliği olan saattir.
Penetrantı tatbik ettiğimizde kurduğumuz saat bizi uyardı.
Sırası gelen işlem Yüzeyde bulunan penetrantı temizleme işlemidir.
PENETRANT FAZLASININ TEMİZLENMESİ
Bizim için önemli olan Süreksizliğin içerisinde kalan Penetrant olduğu için yüzeyde bulunan penetrantı metal yüzeyi görünecek şekilde temizlememiz gereklidir.
Nasıl ki Görülebilme özelliğine göre Tip 1,Tip 2,Tip 3 şeklinde sınıflandırılıyor ise aynı şekilde Temizleme yöntemine görede sınıflandırılırlar.;
Metot A Suyla yıkanabilen penetrantlar
Metot B Sonradan seyreltilen Yağ esaslı penetrantlar
Metot C Solventle temizlenebilen penetrantlar
Metot D Sonradan seyreltilen Su esaslı penetrantlar
Olmak üzere dört guruba ayrılmıştır.
METOT A ( - Water Washable Penetrant.)
Suyla yıkanabilen penetrantların kendi içerisinde seyrelticisi vardır. Sadece su kullanarak yüzey temizliği yapılır.Su parça üzerine tabancayla püskürtülür.Penetrant hattında Su basıncı ve Sıcaklığını ayarlayabileceğimiz sistemin kurulu olması gerekir.Temizlemede kullanacağımız suyun basıncı maksimum 40 Psi, Sıcaklığı ise 10 0 C ile 38 0 C arasında olmalıdır. Su hava yardımıyla pülverize hale getirilip uygulanacaksa hava basıncı maksimum 25 Psi olmalıdır.Parça yüzeyine dik açıda olmayacak şekilde ve minimum 30 Cm uzaklıktan püskürtme işlemi yapılmalıdır.
Uygulama sırasında kaçınılması gereken en önemli işlem yıkama hatası nedeniyle süreksizlik içerisindeki penetrantıda temizlemektir.
Yıkama işleminin Ultraviole Lamba altında yapılması daha kaliteli temiz yüzey elde etmemize yardımcı olur.
METOT B ( - Postemulsifiable Lipophilic Penetrant.)
Sonradan seyreltilen yağ esaslı penetrantlar sadece su kullanılarak yüzeyden arındırılamazlar.Bu nedenle suyla yıkanabilir hale gelebilmesi için Yüzeydeki penetrantın seyreltilmesi gereklidir. (Yağları temizlerkende önce deterjan sonra su kullanıyoruz gibi...) Burada kullanılan seyrelticiye Emülsülfayer denir. Penetrant bekleme süresi tamamlanmış Test parçası yıkanmadan önce Emülsülfayer içine daldırılır,
Emülsülfayer fırçayla veya püskürterek uygulanmaz.Yüzeyde bekleme süresi çok önemlidir.Az beklerse seyreltme işlemini tamamlamadığından metal yüzey rengini elde edemeyiz,Çok beklerse Süreksizlik içindeki penetrantıda seyreltir. küçük süreksizliklerin saptanmasında, suyla yıkanabilir penetrantların yerine sonradan seyreltilen penetrantlar daha etkilidir.
Küçük süreksizlerdeki penetrantı emülsifier ile karışmadığı sürece ayırtma şansı daha az olduğu için, sonradan seyreltilen penetrantlarda yıkama daha az önem taşır. Ne kadar dikkat edilse de suyla yıkanabilir penetrantlar kullanıldığında penetrantı süreksizliğin içinden yıkama olasılığı her zaman vardır.
Her hangi bir standart aksini söylemediği sürece ;
Tip 1 penetrantlarda maksimum yüzeyde bekleme süresi 3 dakikadır .Tip 2 penetrantlarda üreticinin verdiği süre uygulanır.Süre bitiminde seyreltme işlemi Su içerisine daldirilarak veya Tabanca ile su püskürtülerek yapılır. Su basıncı,Sıcaklığı ve Hava basıncı suyla yıkanabilen yani Metot A ile aynıdır.Eğerki aşırı seyreltme olayı gerçekleşmişse parça temizlenir yeniden test işlemine baştan başlanır.
METOT C ( - Solvent Removable Penetrant.)
Solventle temizlenen penetrantların temizlenmesi işleminde,Bekleme süresi sonunda yüzeyde bulunan penetrant önce bezle veya yumuşak kağıtla (Kağıt peçete havlu )olabildiğince silinir amaç yüzeydeki fazlalığı almaktır.Solvent,Remover,aseton ve tiner benzeri solvent bez veya yumuşak kağıda emdirilir.Burada dikkat edilmesi gereken kağıt veya bez lif bırakmayan türden olmalıdır.Kalan lifler bize yanıltıcı belirtiler gösterebilir. Solvent yüzeye püskürterek, dökerek vaya fırçayla uygulanmamalıdır.aşırı kullanımı sonucu süreksizliğin içide temizlenebilir. Buda istenilen bir olay değildir.Yüzey temizliği ne kadar iyi olursa belirtiler o derece net olur.
Tipik solventlere; nafta, Tiner,, Aseton , Perkiloretilen , Isopropil Alkol ve Metilen Klorid örnek olarak gösterilebilirler.
Tip 1 Penetrant temizliğinde Siyah ışık altında temizlik yapmak kontrollu temizlik yapmayı sağlar.
Tip 2 Penetrant temizliğinde ise silme işinde kullandığımız bezin veya kağıdın rengi kontrol edilerek temizlik test edilir.Beze veya kağıda penetrantın rengi çıkmayıncaya kadar kağıt veya bez değiştirilerek temizliğe devam edilir.
Temizleme işlemi önemlidir kalıntı penetrant yanlış karar vermeye neden olabilir.
Tüm Penetrant Metotlarında solventle temizlik yapılabilir.
METOT D ( - Postemulsifiable, Hydrophilic Penetrant.)
Sonradan seyreltilen Su esaslı penetrantlar da aynı yağ esaslı penetrantlar gibi çözünebilmesi yani su ile yıkanabilir hale gelmesi için Emülsülfayer e gerek duyarlar.Su esaslı seyrelticiler deterjan etkisi gösterir.Yıkama suyuna ekleyerek kullanılabilir .Bu şekilde kullanıldığında direk püskürtülerek veya Test parçası seyreltici içine daldırılarak çalkalama işlemi yapılır yapılır.Genellikle Havacılık sektöründe kullanılır.
Şu ana kadar yapmış olduğumuz işlemler;
DEVELOPER UYGULAMASI
Developer kelime olarak ”Geliştirici” anlamındadır.Biz anlatımımızda Developer olarak kullanacağız.
Amaç süreksizliğin içerisinde kalmış olan Penetrantı tekrar yüzeye çıkartıp operatörün görüp değerlendireceği ortamı hazırlamaktır.Bu işlemide kontrast yaratarak yapar.Developerin emici özelliği vardır (Talk pudra) Penetranta temas ettiğinde Penetrant developerin içerisinde harekete geçer bir anlamda Kapiler hareket tersine çalışır.Yüzeyde görünür hale geldiğinde görülen boyut süreksizlikten daha geniş olur nedeni ise penetrantın yüzeyde dağılmasıdır. Developer bekleme süresi arttıkça dağınık görüntüde artar.
Developerlerde kullanım şekli ve yerine göre sınıflandırılmıştır;
Form a Kuru toz Developer
Form b Suya karısabilen(Çözünebilen) Developer
Form c Suda askıda kalan (Çözünmez )
Form d Susuz yaş Developer (Tip 1 için)
Form e Susuz yaş Developer (Tip 2 için)
Form f Özel uygulamalar için developer
Form a Kuru toz Developer
Görülebilir penetrantlarda kullanılmayan kuru toz developer parçanın yüzeyine çok ince bir tabaka şeklinde uygulanır.Görülür penetrant dışında tüm metotlardaki penetrantlarda kullanılabilir.Herhangibir sıvı banyosuna gerek görmemesi ve taşıma kolaylığı gibi avantajı,Temiz hava sistemi,maske kullanımı ve test parçasının uygulama öncesi tamamen kuru olması gibi dezavantajı vardır.
Zehirleyici özelliği yoktur ancak yınede solunum yoluyla almamakta yarar vardır.Özetle kuru toz developer kullanılıyorsa maske takılmalıdır. Kaçınılmasıgereken diğer bir olumsuzluk ise nem dir.Uygulama bölgesinde nem olursa küçük süreksizlikler kaçırılabilir.Kuru developerler farklı şekillerde uygulanabilirler.;
*Plastik elde kullanılan püskürtücü kullanarak,
*Test parçasını içinde kuru toz bulunan kazana daldırarak,
*Hava tabancasıyla püskürterek,
*Yine kazan içinde ama Kazan içinde toz bulutu oluşturarak(Dust chamber)
*Elektrostatik sistem kullanarak
Hangi kullanım şekli uygulanırsa uygulansın dikkat edilmesi gereken ;Developerin ıslanması veya nemlenmesi homojen dağılmayı engeller,Penetrant kalıntılarıda ilgisiz belirtilere neden olur.
Form b Suda çözünmüş Developer
Tanım olarak ;Bu tür developerlerde developer partikülleri su içerisinde erir ve içerisinde ıslatma özelliğini arttırıcı katkı,korozyon önleyici vardır.Kurutma sonucu suyun buharlaşmasıyla developer partikülleri kristalize olur ve Test parçası üzerinde parlak beyaz ince bir film tabakası oluşur.
Yüzeyinde çizgi şeklinde yapılar oluşmaz ve Developeri çalkalama işlemine gerek duymaz.Son temizlik işlemi kolaydır.
Form b developerler gözle görülür ve suyla yıkanabilir penetrantlarda kullanılmaz
İçerisinde kullanılan suya bağlı olarak bakteri oluşabilir.Böyle birşey söz konusu olduğunda developer tamamen atılmalı ve tankın içerisi temizlendikten sonra sonra yeni developer hazırlanmalıdır.
Toz seklinde olan kuru developer tamamen eriyinceye kadar karıştırma işlemi yapılır.Hazırlama yapıldıktan sonra kullanmadan önce 4-5 saat beklemek gereklidir.
Kuru tozun ve suyun hangi oranlarda olması gerektiği üretici tarafından belirtilir.Ancak zamanla buharlaşma nedeniyle yoğunluğu artabilir yoğunluğun ölçülerek (Hidrometre ile) su ilave edilmesi gerekebilir.Veya yoğunluk düşmüşse toz developer ilave edilir.
Sprey şekilde veya daldırma şeklinde kullanılabilir.Daldırma yapıldığında çalkalama işlemine gerek yoktur.
Test işlemi developer tamamen kurumadan yapılmaz.Oda sıcaklığında kuruması çok yavaş olacağından kurutma fırını kullanılır. Kurutma işlemi sonucu parça kontrol edilir.
Form c Suda askıda kalan Developer
Su içerisinde partiküller halinde bulunur ancak suda çözünmezler.İçerisine korozyon önleyici partiküllerin birbirine yapışmasını önleyici katkıların yanısıra bakteriel oluşumu engellemek için katkı maddeleri ilave edilmiştir.Üretici firma tarafından karışım oranı verilmiştir.Birbirinden farklı şiüretici şirketlerin konsantrasyon oranları farklıdır. Su-Toz developer uygun oranda karıştırılarak hazırlanır.Hazırlama işlemi tamamlandıktan sonra 4-5 saat beklemek gereklidiidi
gereklidir.Oda sıcaklığında buharlaşması zor ve geç olacağı için içerisinde sıcak hava sirkülasyonu olan kurutma fırını kullanma zorunluluğu vardır.
Suyla yıkanabilen Penetrant kontrolunda kullanılır.Kullanım öncesi developer partiküllerinin homojen olarak su içerisine dağılımını sağlamak için kesinlikle karıştırma işlemi yapılmalıdır.
Floresan Penetrant hattında kullanım zorunluluğu vardır.
Test parçası Developer içerisinde 30 saniyeden fazla kesinlikle kalmamalıdır.İçerisinde su bulunması nedeniyle uzun süre kalırsa süreksizlik içerisinde bulunan penetrantıda çözebilir.
İç bükey bölgeleri olan test parçalarında uygulama sonrası birikmeleri engelleyecek şekilde konuşlandırıp kurutulmalıdır.
Developer tamamen gurumadan geliştirme görevi başlamaz.Bu nedenle tamamen kurutulmadan kontrol işlemi yapılmamalıdır.
Karışımın buharlaşma sonucu yoğunluğu artarsa su,Test parçasının üzerinde partiküllerin tasınması nedeniyle yoğunluğu azalırsa Toz developer ilave edilir.
HİDROMETRE ÖRNEKLERİ
Hangi işlemin yapılacağına Hidrometreyle ölçüm işlemi yapıldıktan sonra karar verilir
Form d ve Form e Susuz yaş Developer
Susuz yaş tanımından kasıt ;Developer partikülleri hızlı buharlaşabilen solvent içerisinde bulunur.Solvente karışmaz serbes halde bulunur.Genellikle kullanıma hazır halde ayresol kutu içerisinde bulunur.Penetrant testinde yaygın şekilde kullanılan QPL SAE AMS 2644 ( Qualified Products List of Products Qualified Under SAE Aerospace Material Specification AMS 2644 - Inspection Material, Penetrant) ‘ e göre iki gurup olarak sınıflandırılmıştır.
Form d Tip 1 Floresan Penetranta göre formülize edilmiş, Form e ise Tip 2 Görülebilir penetranta göre formülize edilmiştir. Aynı anda her iki tip için kullanılan developerlerde vardır.
Developer ;penetrantla uyumlu olup olmadığına dikkat edilerek seçilir.Solvent developerler en hassas developerlerdir.Bu nedenle küçük süreksizlikleri diğer developer türleriyle karşılaştırdığımızda bulma şansı yüksektir. Kuruma süresi çok kısadır. Dolayısıyla Penetrantı çözme riski yoktur.
Portatif özelliği vardır, Çok çabuk buharlaşma nedeniyle kurutma zamanına gereksinimi yoktur.
Tekrar kazanımı olmadığı ve kapalı olarak bulunduğundan diğer formda olan developerlerde istenmeyen kirlenme veya yabancı madde ihtiva etmek gibi bir risk yoktur.
Uygun teknikle tatbik edildiğinde Düzgün bir yüzey ve istenilen developer tabakası oluşur.Tabakanın kalınlığı operatörün kontrolündedir.
Her iki Tip (Floresan ve Görülür) Penetrant uygulamasında kullanılabilir.ve Hassasiyeti yüksektir.
Olumsuz özellikleri ise;
Yanıcı olabilir,
Uygulama sırasında sağlık açısından buharınısolunum yoluyla almamak gerekir,
Kullanım süresince sıklıkla çalkalamak gerekir,
Küçük sayılabilecek kutularda bulunduğundan Boyut olarak büyük Test parçalarında kullanımı uygun değildir.Küçük alanlarda yapılan testlerde uygundur.
Bazen basıncını kaybedebilir veya püskürtücü nozulun tıkanması ile kullanılmaz hale gelebilir.
Dikkat edilmesi gereken:
Kullanım öncesi tatbik edilecek yüzeyde nem bulunmamalı,
Kendisinden basınçlı olarak imal edildiğinden,Kullanım öncesi istenilen basıncı sağlamak ve developerin kutu içerisinde homojen dağılımını sağlamak için sallayarak çalkalanmalıdır.
Uygulama sırasında yüzeyde ince bir tabaka oluşturulmalıdır.Developer tabakası kalın olursa küçük süreksizlikler görülmeyebilir.
Tip 1 penetrant uygulamasında developer tatbikinden sonra çok hafif bir metal rengi (Test parçasının) algılanamıyorsa Developer kalınlığı fazladır.
Tip 2 Penetrant uygulamasında daha iyi görselliği sağlayabilmek için developer biraz daha kalın olabilir.Bunun karşılaştırmasınıda çatlatılmış Aluminyum panel kullanarak yapabiliriz.
TEST PARÇASINI KURUTMA İŞLEMİ
Test parçası developer tatbik edildikten sonra (Metot c- Form d hariç) kurutulmalıdırki Süreksizlik içerisindeki Penetrant görülebilir hale gelsin.
Kurutma işlemi; İçerisinde sıcak hava sirkülasyonu olan iç ısısı her bölgesinde aynı olan kurutucularda yapılır.Termostat kullanarak ısı aralığı ayarlanabilir olmalıdır.Kullanılan termometre ve termostat kalibreli olmak zorundadır.
Kurutma işlemi oldukça önemlidir.FPI sistemlerinde kullanılan kurutucular 66 0 C ile 107 0 C arasında ayarlanabilir olmalıdır.
Termometre ortam sıcaklığını gösterir ama uygulayıcı için önemli olan test parçasının ulaştığı ısıdır.Test parçası dolayısıyla Developer kurumamış olursa kontrol işlemi yapılamaz, Yine aynı şekilde Kuru toz developer(Form a ) kullanabilmek içinde yüzeyin kuru olması gerekmektedir.
Test parçasının ısısı (Ortamın değil) 60 0 C dereceye ulaşmışsa,Penetrant kurumuş olabileceğinden Test işlemine devam edilmez. Tüm işlem basamaklarına baştan başlanır.Edildiğinde ise küçük süreksizlikleri tesbit etme olanağı yoktur.
Özetle ısı ne kadar artarsa Hassasiyet o kadar azalır.
Test parçası sıcaklığının maksimum 52 0 C ye kadar cıkmasına müsade edilir.Bu sıcaklıkta dahi operatörün çıplak elle tutması sakıncalıdır.
Uygun kurutma işlemiyle ilgili; 49 0 C sıcaklıkta 5 dakika yazmak doğru olmasına rağmen aralıklı olarak yüzeyin kuruyup kurumadığını kontrol ederek ,Kuruduğu anda kurutucudan çıkarmak en garantili işlemdir.Çünki Test parçasının büyüklüğüne , fiziki yapısına ve materyaline bağlı olarak kuruma süresi değişkenlik gösterebilir.
Kurutma işleminde dikkat edilmesi gereken iki değişken ;
Kurutucu ısısı ve Test parçasının kurutucu içerisinde kalma süresi.
Penetrantın gelişme zamanı yani görünür hale gelmesi için gerekli süre genellikle Kurutma sırasında tamamlanmış olur.
Floresan Penetrant hattında kurutucu
TEST PARÇASININ KONTROLU
Parçanın kontrolu Ultraviole lamba ile yapılacaksa (Tip 1 Floresan penetrant kontrolu) burada önemli olan UV lambanın ışık şiddeti ve Karartılmış kabinde test bölgesine gelen beyaz ışık şiddetidir.
Lambanın şiddeti minimum 1000 mW/cm 2 (38.1 cm mesafede)olmalıdır.Test alanına gelen (herhangi bir sızıntı)Beyaz ışık siddeti is 2 fc den fazla olmamalıdır.
Görülebilir penetrant (Tip 2) kontrolu uygulanıyor ise Test ortamındaki aydınlatma minimum 100 fc olmalıdır.
Karanlık kabinde kontrol işlemine başlamadan önce operatör göz adaptasyonunu sağlayıncaya kadar kontrol işlemi yapmamalıdır.
Göz raporunda “gözlüklü çalışabilir “ diyorsa kesinlikle gözlüğünü kullanmalıdır.
Kontrol , işlem basamakları ne kadar özenli yapılmışsa o kadar güvenilir sonuç verir.
Test parçasının yüzeyinde algıladığımız görüntüler gerçek süreksizlik görüntüleri olabileceği gibi gerçeğe yakın yanıltıcı görüntülerde olabilir.Burada operatörün tecrübesi ön plana çıkmaktadır.
Test parçasının imalat yöntemine göre veya serviste üzerine gelen yüklerin yönüne göre operatörde öncelikle bir beklenti oluşmalıdır.
Kullandığı eldivenin temiz olması elinden parça yüzeyine penetrant taşınmasına engel olacaktır.
Dolayısıyla eldivenden kaynaklanan bir ilgisiz belirti oluşmayacaktır.
Tüm istasyonların temizliğine dikkat edilmelidir.Sistemden parça üzerine yapışmış bir ip parçası parçanın üzerinden sonradan düşse bile sanki süreksizlik gibi yanıltıcı görüntü verebilir.
Olabildiğince test parçasının üzerinden Lastik,plastik conta benzeri parçalar kimyasal zarar görmemesi,delik içerisinde bulunan burçlar sökülmelidir.Sökülemiyor ise burçla ana malzeme arasından sızıntı yapan penetrant delik çevresinde oluşan küçük süreksizliklerin tesbitini güçleştirir.Bu nedenle bu tür bölgelerde daha fazla dikkatli kontrol işlemi gerçekleştirilmelidir.
Belirtilerin yorumlanmasında yanlış karar vermekten karar verememek daha güvenlidir .Karar verilemeyen kontrol işleminde ya işlem yeniden yapılır veya ikinci bir yöntemle doğrulama işlemi gerçekleştirilir.
Sonuç raporu yazılır.
TEST PARÇASININ KONTROL SONUCU SON TEMİZLİĞİ
Test işlemi üç farklı şekilde sonuçlandırılabilir;
1 . Süreksizlik tesbit edilmemiştir .Faal olarak (NDT yönüyle) sisteme verilir. Ancak test parçasının temizlenmesi gerekir.Parça yüzeyinde kalan developer ve penetrant artıkları bir sonraki işlem
için ( boyama,kaplama vs) sorun yaratabilir veya korozyona neden olabilir.Temizleme işleminin ne şekilde olacağı uygulanan metota bağlıdır.Developer suyla temizlenebilir ancak Yağ esaslı penetrant kullanılmışsa yağı çözebilmek için buharla temizleme yapılmalıdır.Su esaslı penetrant kullanılmışsa deterjanla temizlemek yeterli olabilir.
2. Süreksizlik tesbit edilmiştir.
a) Süreksizlik tamir kapsamına giriyorsa ;Tamire gönderilir ancak tamir sonrası tekrar kontrola gelmelidir.Temizleme işlemi ikinci kontrolda sorun çıkmazsa yapılır.
b) Süreksizlik sartnameye göre tamirlik değil ve limit dışı ise atılacaktır.Burada dikkat edilmesi gereken herhangibir karışıklık yada hata sonucu sisteme geri dönmemesi için gerekli tedbirin alınması gerekir.(Boyamak,Kırmak,taşlamak vs) Bu durumda son temizleme işlemi yapılmayabilir.
TEST PARÇASINDA BULUNAN BELİRTİLERİN KAYIT ALTINA ALINMASI
Belirtilerin kayıt altına alınması istenirse en basit yöntem fotoğrafını çekerek rapora eklemektir.Bunun dışında görüntü bir bant üzerine nakledilerek veya önce üzerine vernik kuruduktan sonra vernikle beraber kaldırılarak görüntünün taşınma işlemi yapılabilir.
SIVI PENETRANT TESTİNDE KULLANILAN TECHİZATLAR:
1.Mobil yani portatif techizatlar.
2.Sabit yani Atölyede kullanılan techizatlar.
Mobil techizatlarıda a) Flouresan Penetrant portatif kit,
b) Görülebilir Penetrant kit olarak sınıflandırabiliriz.
Flouresan Penetrant portatif Kit Görülebilir penetrant portatif Kit
Flouresan Penetrant Kit içerisinde Penetrant,Developer,Solvent temizleyici temizleme Bez veya kağıtlar işaretleme kalemi veUV lamba bulunur.
Bu kitle iş yapıldığında;
Tip 1,Metot C ve Form d şeklinde tanım yapabiliriz.
Görülebilir Penetrant Kit içerisinde ise Penetrant,Solvent temizleyici,Developer,Aydınlatma feneri ,Temizlik için bez veya kağıt,İşaretleme kalemi bulunur.
Tip 2 Metot C Form d şeklinde tanım yapabiliriz.
Her iki kit içinde gerekli olan birinci kural,Kullanılan malzemenin MSDS(Materyal safety data sheet) inin bulunması ,son kullanım tarihlerine uyum,Kullanılan UV nin standartlara uygun ışık şiddetinde bulunmasıdır.
Sabit Flouresan Penetrant Hatları :
Genelde kontrol sayısı yüksek işletmelerde kullanılır.İlk yatırım maliyeti ve işletme maliyeti yüksektir.Kurutma ,Kontrol kabini aynı ancak Developer uygulama şekli ( Form),Penetrant tipi (Metot) ne bağlı olarak istasyon sayısı farklılıklar gösterir.
Standartlara uygun Flouresan Penetrant hattında neler olması gerektiği ve yapılması gereken proses kontrollar ayrıca incelenecektir.
Hattın iş istasyonu sıralamasını kendinize göre metot ve formları değiştirerek yapınız....
Metot A Suyla yıkanabilen penetrant kontrolunda iş akış şeması
Metot B Sonradan seyreltilen Yağ esaslı penetrant kontrolunda iş akış şeması
Metot C Solventle temizlenebilen penetrant kontrolunda iş akış şeması
Metot D Sonradan seyreltilen Su esaslı penetrant kontrolunda iş akış şeması
PROSES KONTROLLAR
Yapılan test işleminin güvenilir olabilmesi için Test işleminde kullandığımız techizat ve materyallerin istenilen şartları sağlayıp sağlamadığının kontrolu işlemine proses kontrol denir.
Proses kontrollar peryodik olarak yapılmalıdır.Kontrol peryodu sistemin çalışma yoğunluğuna bağlı olarak değişebilir.Üç vardiya çalışan bir FPI hattında bazı kontrol işlemleri her vardiya başlangıcında yapılacağı gibi aralıklı kullanılan bir sistemde kullanım öncesi kontrollar yapılır.
Yeni malzeme satın alınıyorsa;O malzemelerin (Penetrant,Developer,Emulsulfayer,UV lamba vs)
Hangi standarda uygun üretildiği ve O standardında bizim çalışma standardımızda olup olmadığının kontrolu gerekir.
Alınan malzemelerin Teknik Belgeleri Bir dosya içerisinde muhafaza edilmelidir.
Peryodik yapılan (Kullanıcı tarafından veya Kalibre merkezinde yaptırılan) kalibrelerinde kalibre sonuçlarının dosya içerisinde muhafazası ,Kalibre etiketlerininde görülebilir şekilde Techizat üzerinde bulunması gerekir.
Aşagıda örnek Proses kontrollar anlatılacaktır.Ancak bunlar genel olup ; Kullanıcı kendi kullandığı standardın Proses kontrollarını uygulamalıdır.
Penetrant kirlilik Testi:
Penetrant sıvısına giren Test malzemesi ne kadar iyi temizlenmiş olursa olsun üzerinde bazı partiküller taşıyabilir ve penetranta karışabilir.Yada açık sistem olması nedeniyle çevreden kirlenme olabilir.Bu nedenle penetrantın kontrolunda içerisinde Bulanık beyazlaşma zeminde partiküller görülürse sistemin tamamen boşaltılıp ,Kazan temizlenip yeni penetrantın kullanıma alınması gerekir.Hergün yapılması gereken işlemdir.
Penetrant Parlaklık ve Su Testi:
Bu test işleminin yapılabilmesi için,Sisteme koyulan kullanılmamış penetranttan belirli miktarda temiz kap içerisine master penetrant (1 litre) ayrılır.Yapılan test ,Sistemde kullanılan penetrantla kullanılmamış arasında karsılaştırma yapılarak gerçekleştirilir.Test yapacak techizat yoksa kalibre merkezinde gerçekleştirilir.
Örneğin; ASTM E 1417 Standardına göre Penetrant içerisinde su miktarı %5 den fazla olmamalı Parlaklığı ise %90 dan aşağıda olmamalıdır.Test peryodu ise Parlaklık testi için 3 ay,Su konsantrasyon testi 1 aydır.
Sadece su miktarı yüksek çıkmışsa oranı aşağıya çekebilmek için penetrant ilavesi yapılabilir.
Yağ esaslı Emulsifayer Su konsantrasyon testi:
Emülsifayer içerisine her hangi bir şekilde karışan su miktarı %5 den fazla olmamalıdır.Eğer fazla olursa atılmalı .sistem temizlendikten sonra yeni Emulsüfayer konulmalıdır.
Yıkama istasyonu kontrolları:
Yıkama istasyonunda kullanılan Su basıncı 40 Psı den yüksek,Sıcaklığı ise 10 0 C - 38 0 C arasında olmalıdır.Sistemde pülverize için hava kullanılıyorsa; Hava basıncı 25 Psı den fazla olmamalıdır.
Yukarıda bulunan değerleri sağlayabilmemiz için Sistemde;
-Su basınç saati,Su sıcaklık saati,Hava basınç saati bulunmalı sıcaklık ve basınç ayarlanabilmelidir.Kullanım öncesi kontrol edilmelidir.
Ancak ayarlanılan değerlerin doğru olduğundan emin olabilmemiz için Tüm kullanılan saatlerin kalibreli olması,Etiketlerinin üzerinde kalibre tarihleri ve bir sonraki kalibre tarihlerinin bulunması gerekir.
Kalibre peryotları 6 ay dır.
Developerler istasyonu testleri:
Sistemde kuru developer kullanılıyorsa ve hava ile puskürtülüyorsa ;Hava basıncı 5 Psı nin üzerinde olmamalıdır.Yina hava basıç saati kalibreye gönderilmelidir.
Kirlilik testi için;
10 boyunda temiz panele püskürtme yapılır .Bu mesafe içinde noktasal olmak kaydıyla 10 taneden fazla kalıntı görülmemelidir.Görülürse sistem temizlenir.Yeni developer konulur.
Sistemde sulu developer kullanılıyorsa;
8cmx 25cm boyutunda temiz bir Aluminyum panel developere daldırılacak,Kurutma işleminden sonra yüzeyde uniform bir yapı oluşmuyorsa ve floresan bir görüntü oluşuyorsa developer boşaltılıp yeni developer sisteme konulacaktır.
Yoğunluk testi için;
Karışımda developer ve su oranları üreticinin verdiği oranda olmalıdır.Yoğunluk testi Hidrometre kullanılarak yapılır.yoğunluk düşükse;Developer ilave edilir,Yüksekse su ilave edilir.İşleme istenilen yoğunluk elde edilinceye kadar devam edilir.
Penetrant Sistem Performans Testi;
Bu test işlemi Penetrantın ve Emulsifayer in yıkanabilirliğinin kontrolunu ve penetrantın hassasiyetinin kontrolunu içerir.
Yardımcı techizat olarak,Bilinen çatlaklar içeren test paneli,Kumlanmış yüzeyi olan panel,Kullanımdaki Penetrant ve Emülsifayer ,Kullanılmamış Penetrant ve Emülsifayer.
İşlemin temel felsefesi sistemde kullanılan ve kullanılmamış Emülsifayer ve Penetrantla aynı işlemleri yapıp birbirine yakın sonucu elde etmektir.Elde edilemez ise sistem temizlenir,yeni Emülsifayer ve penetrant sisteme konur.
Bu işlemler için PSM 5 Tam panel kullanılabilir.Panel üzerinde 5 adet farklı bilinen çatlak ve kumlanmış alan vardır.
Kurutma istasyonu testi:
Test parçasının kurutulması işlemi önemlidir.Kurutucu maksimum 71 0 C ısı verebilmeli ve verdiği ısı ayarlanabilmelidir.
Termostatın ve Termometrenin her 3 Ayda kalibreye gitmesi gereklidir.
Kontrol istasyonu (Karanlık oda) testi:
Kontrol istasyonu testi oda içerisinde Ultraviole lambanın ve Kabin içesine herhangi bir şekilde sızan beyaz ışık şiddetinin ölçümüdür.
Siyah ışık şiddeti 38cm mesafeden ışık demetinin merkezinde minimum 1000 mW/cm 2 olmalıdır.
(Lamba zamana bağlı olarak ışık şıddetini kaybeder.)
Fiziksel kontrolu ve ışık siddet kontrolu her gün yapılmalıdır.
Işık ölçerlerde her yıl kalibreye gönderilmelidir.
Test parçasının kontrol edildiği noktada ise beyaz ışık 2fc (foot candle) den fazla olmamalıdır.
(NOT : Karanlık odada havalandırma sistemi bulunmalıdır.)
İmalat Şekilleri ve Karşılabilecek Süreksizlikler
İmalat sürecini aşağıda görüldüğü üzere örneklendirebiliriz.İmalat yöntemi ne olursa olsun Penetrant kontrolu uygulayabileceğimiz tek süreksizlik tipi yüzeye açılan süreksizliklerdir.
Penetrant kontrolunun olumsuz yönü yada başka deyimle sınırlamaları;
-Sadece yüzeye açılan süreksizlikler,
-Aşırı gözenekli yapıdaki malzemeler.
Sonuç olarak bir malzemeye Penetrant test işlemi uygulandığında sadece yüzeyi ile ilgili bilgi sahibi olabiliriz.
Kontrol işlemini her üretim istasyonunda uygulayabileceğimiz gibi ,En son aşamada da uygulayabiliriz buna işletmenin kalite birimi karar verir.
Bazı dokümanlarda süreksizlik görüntüleriyle ilgili tariflerde yapılır ancak ;
Operatörün başarısını Tecrübe belirler.
Deneyim ,test sayısının artmasıyle,Farklı imalat şekli ve farklı malzemelerin testiyle pekişir.
Tüm yukardaki üretim şekillerinde karşılaşabileceğimiz süreksizlik tipleri,
►Nonmetalik kalıntılar (Nonmetallic inclusions)
►Gözenek (Porosity)
►Nonmetalik kalıntı izleri (Stringers)
►Dikişler (Seams)
►Dövme katlanmaları (Forging Laps)
►Isıl işlem çatlakları (Heat Treat Cracks)
►Dövme patlama veya çatlakları (Forging Burst, Cracks)
►Soğuk yırtılma (Cold Shuts)
►Çekme çatlakları (Shrink Cracks)
►Üfürüm boşlukları (Blow Holes)
►Taşlama çatlakları (Grinding Cracks)
►Yorulma çatlakları (Fatigue Cracks)
Kaynaklarda oluşabilecek hata türlerine örneklemeler:
►Krater çatlakları (Crater Cracks)
►Çekme çatlakları (Shrink Cracks)
►Gözenek (Porosity)
►Nonmetalik kalıntılar (Non Metallic İnclusions)
“Sıvı Penetrant Test işlemi; Sadece yüzeye açık olan süreksizlikleri tesbit etmekte kullanılan ,Tahribatsız muayene yüzey yöntemlerinden birisidir”
Yazar : Sedat Nevzat Aras NDT lvl:3